快速導(dǎo)航Product Center
EVA開(kāi)片機(jī)
橡膠冷片機(jī)
碳酸鈣填充造粒機(jī)
雙螺桿水拉條造粒機(jī)
橡塑密煉機(jī)
片材擠出機(jī)
橡膠切膠機(jī)
開(kāi)煉機(jī)
低煙無(wú)鹵密煉雙階
EVA汽車(chē)內(nèi)飾密煉擠出
EVA電熱式熔接機(jī)
實(shí)驗(yàn)室小密煉機(jī),小煉膠機(jī)
振德隆機(jī)械(昆山)有限公司
手機(jī):18626186560
地址:江蘇省昆山市花橋鎮(zhèn)象蚌涇路28號(hào)
聯(lián)系人:孫先生
開(kāi)煉機(jī)
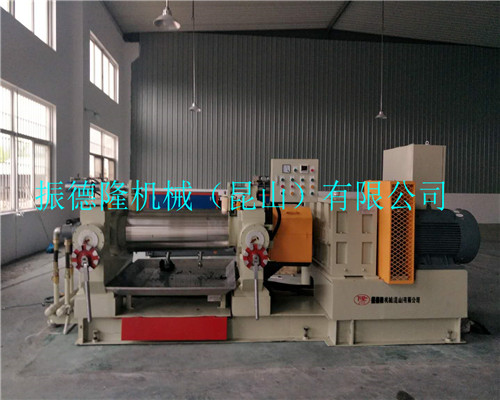
18寸開(kāi)煉機(jī)
【附件下載】:資料下載
【產(chǎn)品特點(diǎn)】:混煉常用的設(shè)備是開(kāi)煉機(jī)和密煉機(jī)。
①開(kāi)煉機(jī)混煉 開(kāi)煉機(jī)混煉的必要條件是根據(jù)各種橡膠的粘彈性、松弛時(shí)間和轉(zhuǎn)變溫度等基本性質(zhì),選擇合適的輥溫(下表),使之處于包輥狀態(tài),以便進(jìn)行混煉。
各種橡膠開(kāi)煉機(jī)混煉的適用溫度
膠 種 輥溫,℃ 膠 種 輥溫,℃
前 輥 后 輥 前 輥 后 輥
天然橡膠 55~60 50~55 氯醚橡膠 70~75 85~90
丁苯橡膠 45~50 50~60 氯磺化聚乙烯 40~70 40~70
丁腈橡膠 35~45 40~50 氯丁橡膠 ≤40 ≤45
丁基橡膠 40~45 55~60
丙烯酸酯橡膠 40~55 30~50
順丁橡膠 40~60 40~60 聚胺酯橡膠 50~60 55~60
乙丙橡膠 60~75 約85 聚硫橡膠 45~60 40~50
加料順序是影響開(kāi)煉機(jī)混煉質(zhì)量的一個(gè)重要因素。
加料順序不當(dāng)會(huì)導(dǎo)致分散不均勻,脫輥、過(guò)煉,甚至發(fā)生早期硫化(焦燒)等質(zhì)量問(wèn)題。原則上應(yīng)根據(jù)配方中配合劑的特性和用量來(lái)決定加料順序,宜先加量少、難分
散者。后加量大,易分散者;硫黃或者活性大、臨界溫度低的促進(jìn)劑(如超速促進(jìn)劑)則在最后加入,以防止出現(xiàn)早期硫化(焦燒)。液體軟化劑一般在補(bǔ)強(qiáng)填充劑等
粉劑混完后再加入,以防止粉劑結(jié)團(tuán)、膠料打滑、膠料變軟致使剪切力小而不易分散。
橡膠包輥后,按下列一般的順序加料:橡膠、再生膠、各種母煉膠→固體軟化劑(如較難分散的松香、硬脂酸、固體古馬隆樹(shù)脂等)→小料(促進(jìn)劑、活性劑、防
老劑)→補(bǔ)強(qiáng)填充劑→液體軟化劑→硫黃→超促進(jìn)劑→薄通→倒膠下片。
對(duì)于某些特殊膠料(如硬質(zhì)膠、海綿膠等),則需采取與上述一般加料順序不同的混煉方法。
除了輥溫和加料順序影響開(kāi)煉機(jī)混煉質(zhì)量之外,在操作上尚需注意:填膠容量不宜過(guò)多,否則不易混煉均勻,一般合成膠容量應(yīng)比天然橡膠小一些。在保證混煉質(zhì)
量的前提下,混煉時(shí)間應(yīng)盡量縮短,以防止膠料因過(guò)煉而導(dǎo)致物理機(jī)械性能下降和影響生產(chǎn)效率。輥筒速度和速比要適宜,既要有利于混合、分散,又不致因生熱過(guò)快
導(dǎo)致早期硫化(焦燒)。
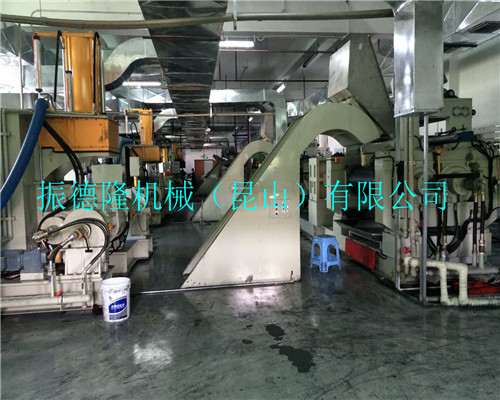
②密煉機(jī)混煉 密煉機(jī)通過(guò)轉(zhuǎn)子、上下頂栓在密煉室中產(chǎn)生復(fù)雜的流動(dòng)方式和高剪切力,使橡膠配合劑和粒狀添加劑很快粉碎和均勻分散,是一種高效的混煉方法。
但是高剪切力會(huì)使物料溫度在混煉中迅速上升,一般會(huì)達(dá)到130℃。這已超過(guò)了大多數(shù)硫化系統(tǒng)的活化溫度,會(huì)使膠料發(fā)生早期硫化(焦燒)。一般的做法是將大部分
物料在密煉機(jī)中混煉,然后將膠料從密煉機(jī)排放到開(kāi)煉機(jī)上,在開(kāi)煉機(jī)上加硫化劑或超速促進(jìn)劑。由于開(kāi)煉機(jī)實(shí)際上只在輥縫線(xiàn)上對(duì)膠料有擠壓作用,而提供了很大的
冷卻面積,致物料的溫度降低。在這一階段加入硫化劑可以避免膠料發(fā)生早期硫化(焦燒)。
①開(kāi)煉機(jī)混煉 開(kāi)煉機(jī)混煉的必要條件是根據(jù)各種橡膠的粘彈性、松弛時(shí)間和轉(zhuǎn)變溫度等基本性質(zhì),選擇合適的輥溫(下表),使之處于包輥狀態(tài),以便進(jìn)行混煉。
各種橡膠開(kāi)煉機(jī)混煉的適用溫度
膠 種 輥溫,℃ 膠 種 輥溫,℃
前 輥 后 輥 前 輥 后 輥
天然橡膠 55~60 50~55 氯醚橡膠 70~75 85~90
丁苯橡膠 45~50 50~60 氯磺化聚乙烯 40~70 40~70
丁腈橡膠 35~45 40~50 氯丁橡膠 ≤40 ≤45
丁基橡膠 40~45 55~60
丙烯酸酯橡膠 40~55 30~50
順丁橡膠 40~60 40~60 聚胺酯橡膠 50~60 55~60
乙丙橡膠 60~75 約85 聚硫橡膠 45~60 40~50
加料順序是影響開(kāi)煉機(jī)混煉質(zhì)量的一個(gè)重要因素。
加料順序不當(dāng)會(huì)導(dǎo)致分散不均勻,脫輥、過(guò)煉,甚至發(fā)生早期硫化(焦燒)等質(zhì)量問(wèn)題。原則上應(yīng)根據(jù)配方中配合劑的特性和用量來(lái)決定加料順序,宜先加量少、難分
散者。后加量大,易分散者;硫黃或者活性大、臨界溫度低的促進(jìn)劑(如超速促進(jìn)劑)則在最后加入,以防止出現(xiàn)早期硫化(焦燒)。液體軟化劑一般在補(bǔ)強(qiáng)填充劑等
粉劑混完后再加入,以防止粉劑結(jié)團(tuán)、膠料打滑、膠料變軟致使剪切力小而不易分散。
橡膠包輥后,按下列一般的順序加料:橡膠、再生膠、各種母煉膠→固體軟化劑(如較難分散的松香、硬脂酸、固體古馬隆樹(shù)脂等)→小料(促進(jìn)劑、活性劑、防
老劑)→補(bǔ)強(qiáng)填充劑→液體軟化劑→硫黃→超促進(jìn)劑→薄通→倒膠下片。
對(duì)于某些特殊膠料(如硬質(zhì)膠、海綿膠等),則需采取與上述一般加料順序不同的混煉方法。
除了輥溫和加料順序影響開(kāi)煉機(jī)混煉質(zhì)量之外,在操作上尚需注意:填膠容量不宜過(guò)多,否則不易混煉均勻,一般合成膠容量應(yīng)比天然橡膠小一些。在保證混煉質(zhì)
量的前提下,混煉時(shí)間應(yīng)盡量縮短,以防止膠料因過(guò)煉而導(dǎo)致物理機(jī)械性能下降和影響生產(chǎn)效率。輥筒速度和速比要適宜,既要有利于混合、分散,又不致因生熱過(guò)快
導(dǎo)致早期硫化(焦燒)。
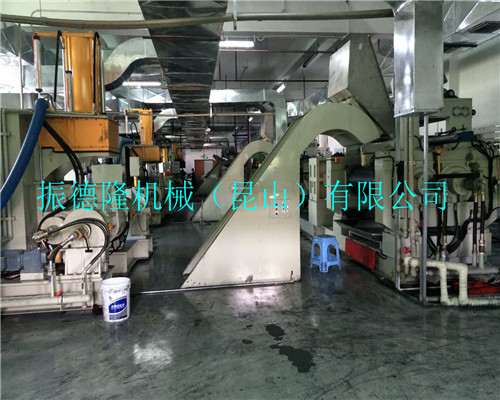
②密煉機(jī)混煉 密煉機(jī)通過(guò)轉(zhuǎn)子、上下頂栓在密煉室中產(chǎn)生復(fù)雜的流動(dòng)方式和高剪切力,使橡膠配合劑和粒狀添加劑很快粉碎和均勻分散,是一種高效的混煉方法。
但是高剪切力會(huì)使物料溫度在混煉中迅速上升,一般會(huì)達(dá)到130℃。這已超過(guò)了大多數(shù)硫化系統(tǒng)的活化溫度,會(huì)使膠料發(fā)生早期硫化(焦燒)。一般的做法是將大部分
物料在密煉機(jī)中混煉,然后將膠料從密煉機(jī)排放到開(kāi)煉機(jī)上,在開(kāi)煉機(jī)上加硫化劑或超速促進(jìn)劑。由于開(kāi)煉機(jī)實(shí)際上只在輥縫線(xiàn)上對(duì)膠料有擠壓作用,而提供了很大的
冷卻面積,致物料的溫度降低。在這一階段加入硫化劑可以避免膠料發(fā)生早期硫化(焦燒)。
混煉常用的設(shè)備是開(kāi)煉機(jī)和密煉機(jī)。
①開(kāi)煉機(jī)混煉 開(kāi)煉機(jī)混煉的必要條件是根據(jù)各種橡膠的粘彈性、松弛時(shí)間和轉(zhuǎn)變溫度等基本性質(zhì),選擇合適的輥溫(下表),使之處于包輥狀態(tài),以便進(jìn)行混煉。
各種橡膠開(kāi)煉機(jī)混煉的適用溫度
膠 種 輥溫,℃ 膠 種 輥溫,℃
前 輥 后 輥 前 輥 后 輥
天然橡膠 55~60 50~55 氯醚橡膠 70~75 85~90
丁苯橡膠 45~50 50~60 氯磺化聚乙烯 40~70 40~70
丁腈橡膠 35~45 40~50 氯丁橡膠 ≤40 ≤45
丁基橡膠 40~45 55~60
丙烯酸酯橡膠 40~55 30~50
順丁橡膠 40~60 40~60 聚胺酯橡膠 50~60 55~60
乙丙橡膠 60~75 約85 聚硫橡膠 45~60 40~50
加料順序是影響開(kāi)煉機(jī)混煉質(zhì)量的一個(gè)重要因素。
加料順序不當(dāng)會(huì)導(dǎo)致分散不均勻,脫輥、過(guò)煉,甚至發(fā)生早期硫化(焦燒)等質(zhì)量問(wèn)題。原則上應(yīng)根據(jù)配方中配合劑的特性和用量來(lái)決定加料順序,宜先加量少、難分散者。后加量大,易分散者;硫黃或者活性大、臨界溫度低的促進(jìn)劑(如超速促進(jìn)劑)則在最后加入,以防止出現(xiàn)早期硫化(焦燒)。液體軟化劑一般在補(bǔ)強(qiáng)填充劑等粉劑混完后再加入,以防止粉劑結(jié)團(tuán)、膠料打滑、膠料變軟致使剪切力小而不易分散。
橡膠包輥后,按下列一般的順序加料:橡膠、再生膠、各種母煉膠→固體軟化劑(如較難分散的松香、硬脂酸、固體古馬隆樹(shù)脂等)→小料(促進(jìn)劑、活性劑、防老劑)→補(bǔ)強(qiáng)填充劑→液體軟化劑→硫黃→超促進(jìn)劑→薄通→倒膠下片。
對(duì)于某些特殊膠料(如硬質(zhì)膠、海綿膠等),則需采取與上述一般加料順序不同的混煉方法。
除了輥溫和加料順序影響開(kāi)煉機(jī)混煉質(zhì)量之外,在操作上尚需注意:填膠容量不宜過(guò)多,否則不易混煉均勻,一般合成膠容量應(yīng)比天然橡膠小一些。在保證混煉質(zhì)量的前提下,混煉時(shí)間應(yīng)盡量縮短,以防止膠料因過(guò)煉而導(dǎo)致物理機(jī)械性能下降和影響生產(chǎn)效率。輥筒速度和速比要適宜,既要有利于混合、分散,又不致因生熱過(guò)快導(dǎo)致早期硫化(焦燒)。
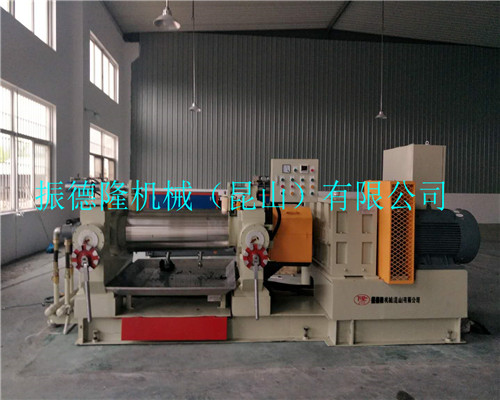
②密煉機(jī)混煉 密煉機(jī)通過(guò)轉(zhuǎn)子、上下頂栓在密煉室中產(chǎn)生復(fù)雜的流動(dòng)方式和高剪切力,使橡膠配合劑和粒狀添加劑很快粉碎和均勻分散,是一種高效的混煉方法。但是高剪切力會(huì)使物料溫度在混煉中迅速上升,一般會(huì)達(dá)到130℃。這已超過(guò)了大多數(shù)硫化系統(tǒng)的活化溫度,會(huì)使膠料發(fā)生早期硫化(焦燒)。一般的做法是將大部分物料在密煉機(jī)中混煉,然后將膠料從密煉機(jī)排放到開(kāi)煉機(jī)上,在開(kāi)煉機(jī)上加硫化劑或超速促進(jìn)劑。由于開(kāi)煉機(jī)實(shí)際上只在輥縫線(xiàn)上對(duì)膠料有擠壓作用,而提供了很大的冷卻面積,致物料的溫度降低。在這一階段加入硫化劑可以避免膠料發(fā)生早期硫化(焦燒)。
①開(kāi)煉機(jī)混煉 開(kāi)煉機(jī)混煉的必要條件是根據(jù)各種橡膠的粘彈性、松弛時(shí)間和轉(zhuǎn)變溫度等基本性質(zhì),選擇合適的輥溫(下表),使之處于包輥狀態(tài),以便進(jìn)行混煉。
各種橡膠開(kāi)煉機(jī)混煉的適用溫度
膠 種 輥溫,℃ 膠 種 輥溫,℃
前 輥 后 輥 前 輥 后 輥
天然橡膠 55~60 50~55 氯醚橡膠 70~75 85~90
丁苯橡膠 45~50 50~60 氯磺化聚乙烯 40~70 40~70
丁腈橡膠 35~45 40~50 氯丁橡膠 ≤40 ≤45
丁基橡膠 40~45 55~60
丙烯酸酯橡膠 40~55 30~50
順丁橡膠 40~60 40~60 聚胺酯橡膠 50~60 55~60
乙丙橡膠 60~75 約85 聚硫橡膠 45~60 40~50
加料順序是影響開(kāi)煉機(jī)混煉質(zhì)量的一個(gè)重要因素。
加料順序不當(dāng)會(huì)導(dǎo)致分散不均勻,脫輥、過(guò)煉,甚至發(fā)生早期硫化(焦燒)等質(zhì)量問(wèn)題。原則上應(yīng)根據(jù)配方中配合劑的特性和用量來(lái)決定加料順序,宜先加量少、難分散者。后加量大,易分散者;硫黃或者活性大、臨界溫度低的促進(jìn)劑(如超速促進(jìn)劑)則在最后加入,以防止出現(xiàn)早期硫化(焦燒)。液體軟化劑一般在補(bǔ)強(qiáng)填充劑等粉劑混完后再加入,以防止粉劑結(jié)團(tuán)、膠料打滑、膠料變軟致使剪切力小而不易分散。
橡膠包輥后,按下列一般的順序加料:橡膠、再生膠、各種母煉膠→固體軟化劑(如較難分散的松香、硬脂酸、固體古馬隆樹(shù)脂等)→小料(促進(jìn)劑、活性劑、防老劑)→補(bǔ)強(qiáng)填充劑→液體軟化劑→硫黃→超促進(jìn)劑→薄通→倒膠下片。
對(duì)于某些特殊膠料(如硬質(zhì)膠、海綿膠等),則需采取與上述一般加料順序不同的混煉方法。
除了輥溫和加料順序影響開(kāi)煉機(jī)混煉質(zhì)量之外,在操作上尚需注意:填膠容量不宜過(guò)多,否則不易混煉均勻,一般合成膠容量應(yīng)比天然橡膠小一些。在保證混煉質(zhì)量的前提下,混煉時(shí)間應(yīng)盡量縮短,以防止膠料因過(guò)煉而導(dǎo)致物理機(jī)械性能下降和影響生產(chǎn)效率。輥筒速度和速比要適宜,既要有利于混合、分散,又不致因生熱過(guò)快導(dǎo)致早期硫化(焦燒)。
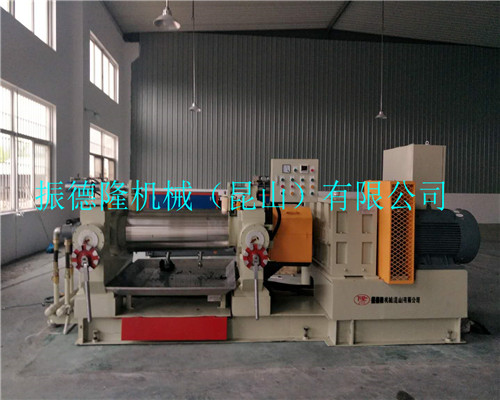
②密煉機(jī)混煉 密煉機(jī)通過(guò)轉(zhuǎn)子、上下頂栓在密煉室中產(chǎn)生復(fù)雜的流動(dòng)方式和高剪切力,使橡膠配合劑和粒狀添加劑很快粉碎和均勻分散,是一種高效的混煉方法。但是高剪切力會(huì)使物料溫度在混煉中迅速上升,一般會(huì)達(dá)到130℃。這已超過(guò)了大多數(shù)硫化系統(tǒng)的活化溫度,會(huì)使膠料發(fā)生早期硫化(焦燒)。一般的做法是將大部分物料在密煉機(jī)中混煉,然后將膠料從密煉機(jī)排放到開(kāi)煉機(jī)上,在開(kāi)煉機(jī)上加硫化劑或超速促進(jìn)劑。由于開(kāi)煉機(jī)實(shí)際上只在輥縫線(xiàn)上對(duì)膠料有擠壓作用,而提供了很大的冷卻面積,致物料的溫度降低。在這一階段加入硫化劑可以避免膠料發(fā)生早期硫化(焦燒)。